三维RPS、MCP在新车型开发中的应用
- 来源:汽车工艺师 smarty:if $article.tag?>
- 关键字:同步工程,RPS,MCP smarty:/if?>
- 发布时间:2020-10-08 08:40
摘要:分析介绍了同步工程中RPS、MCP设计的一般流程、设计原则及内容,提出二维设计在设计过程中出现的问题,结合实践经验,展示了新型三维设计在RPS、MCP设计中的应用,并结合实际案例进一步说明了三维RPS、MCP在设计中存在的优势。
关键词:同步工程;RPS;MCP
随着我国汽车市场的发展,汽车换代不断加快,汽车开发周期不断缩短,同时要求车身尺寸质量水平同步提升。现代汽车制造中,普遍采用车身制造综合误差指数CII(Continuous Improvement Indicator)来控制车身制造质量,即2mm工程。2mm(6σ)应用于汽车工业不仅可以实现经济的汽车制造,同时也是国家制造技术水平的综合反映。自从RPS、MCP引进国内汽车市场后,经过近年来的不断发展,成为汽车行业内产品开发和工艺开发最为重要的基础技术之一。RPS、MCP理论的充分应用与完善,以及焊装SE水平、冲压件制造、夹具设计制造水平的提高,极大地推动了国内车身制造水平的发展。
然而在新车型开发过程中,车身零件RPS、MCP的设计,采用传统二维的设计形式,设计周期长、效率低,若需调整优化较为繁琐,且需要设计人员有较好的三维空间能力,影响了RPS、MCP的设计、评审等工作的开展。如何提升RPS、MCP工作开展的效率,缩短设计周期,业内一直都在探索。目前,结合已开发新车型的尝试,三维设计形式的RPS、MCP将很好地解决此问题,以下将进行阐述。
RPS、MCP设计流程
1.RPS、MCP概述
RPS(Reference Point System)即定位基准点系统,规定了汽车产品制造各环节(包括模具、夹具、检具、装具及测量等)统一的基准系统。以前后统一、上下继承的形式,保证各个环节上由定位基准变换所产生的尺寸偏差最小的车身基准点系统。RPS的应用优势在于,从设计到生产各个环节中的基准尽量统一,从而减小制造误差,提高车身制造精度。
MCP(Master Control Point)即主要控制点,是产品(冲压件、分总成件、总成件及白车身)质量控制的主要基准点及焊接夹具的基准点,在新车型设计阶段同步完成,可使产品质量波动最小化。MCP贯穿新车型产品设计、冲压、焊接以及白车身检测等生产的整个过程。
三维RPS、MCP设计遵循了二维RPS、MCP设计的设计原则,用三维软件直接在3D车身数据中进行RPS、MCP设计,更加直观,提升了设计、评审等工作的开展效率,简化了二维设计的繁琐形式,设计周期比二维设计缩短了1/3。2.车身零件RPS、MCP设计流程
RPS系统制定分六个步骤,即产品功能的研究、产品公差的研究、RPS的制定、定位基准尺寸的确定、产品公差的计算与绘制产品图样。此六个步骤比较适合用在与周边零件匹配关系较为复杂的内外饰、电器等零件。车身零部件的匹配关系较为简单,且冲压件公差体系已经相当完善,可直接定义RPS点,不必先进行产品功能、产品公差等研究。
李盛良等人在《浅谈车身零部件RPS的设计》中介绍了车身零部件RPS设计流程及其优点。随着同步工程的不断应用实践,结合新车型开发流程及RPS、MCP设计的经验总结,为了更好地保证基准的一致性、继承性等,在该文献中流程的基础上,将RPS、MCP设计流程优化增加了细节部分,如图1所示。
车身零件RPS、MCP设计的具体操作中,按照从总成件—分总成件—单件的设计流程开展,基准依次延续。在初版数据发放开始,就开始进行RPS的概念设计,对新产品数据提出相关要求,并参与到数据修改优化中。
车身零件RPS设计
新车型在RPS设计中,为了保证RPS点在实际生产中能切实使用,车身零件定义RPS点时必须遵循三大原则,即3-2-1原则、网络平行原则和一致性原则。
1.3-2-1原则
每个刚性物体(刚体)在空间运动中有6个自由度,即3个沿着坐标系的轴线移动和3个围绕坐标轴的转动。在零部件装配生产时,要确定零部件位置,就需要限制此零部件的6个自由度,才能保持平衡。三维空间自由度及零部件RPS的定位如图2所示,零部件不在同一直线上的定位支撑点A1、A2、A3限制3个自由度(沿Z轴的移动自由度、绕X轴转动的自由度、绕Y轴转动的自由度),定位圆孔B限制2个自由度(沿X轴的移动自由度、沿Y轴的移动自由度),定位长圆孔C限制1个自由度(绕Z轴转动的自由度),零部件空间的6个自由度都得到了控制,称为3-2-1定位原则。
3-2-1定位原则,适用于绝大多数零部件的定位,但对于尺寸较大、刚度不足的零件,在保证了3-2-1定位规则的前提下,还需要根据需要,在RPS定位基准设计中,增加相关定位点来保证零件的平衡状态。特殊形状的零部件并不遵循3-2-1定位原则,如球体定位只需要3个自由度即可达到平衡,旋转体定位需要确定5个自由度即达到平衡,而铰接零件定位需要确定的自由度多于6个,即需要增加定位才能达到平衡状态。
2.网络平行原则
车身零部件RPS设计基于整车网络坐标系下开展,如图3所示。整车网络坐标系是为了精确定位整车上任意一点的空间位置而构造的笛卡儿直角坐标系,前轮理论中心线中点为整车网络坐标系零点,长度(X轴)坐标系、宽度(Y轴)坐标系、高度(Z轴)坐标系都过前轮理论中心线中点。
在整车坐标系内,平行于X轴、Y轴和Z轴的直线在理论上将整车划分为一个个立体网格(原则为100的整数倍)。这些立体网格在正投影面上的投影,反映到设计图样上,即为汽车车身设计所依据的坐标网格线。通过间隔线可以确定汽车上每个点的位置。也就是说,通过与网格线的相对位置,可以确定零部件的位置。
3.一致性原则
一致性原则是指RPS系统必须在汽车车身冲压单件的生产、冲压件分总成的组装焊接、车身总成件的总装以及汽车制造质量控制过程中得到全方面的应用。RPS系统的主旨是通过避免基准转变来保证制造工艺过程的可靠性,以及产品的精度和质量。RPS系统的一致性原则,要求从产品开发阶段直到SOP,RPS点的使用贯彻始终,但增加的辅助RPS点,装配时不在一致性原则范围内。
一致性原则对RPS点的选择与布置要求如下:
1)优先选择孔作为基准点,其次是平面,最后是棱边。2)RPS点必须定位于零件的稳定区域,即冲压零件冲压质量好、在后续焊装过程中不会改变的区域。3)选择RPS点不仅要考虑单件加工的要求,而且还要考虑以后装配过程的要求。
4)分总成的RPS点优先选择尺寸较大的零件RPS点,构成分总成的RPS点系统。
5)分总成/总成的RPS点要根据3-2-1原则、网格平行性原则、分总成自身的结构、工艺和功能特点,从组成零件的RPS点中选择分总成/总成的RPS点。
4.RPS设计应用
传统的RPS设计采用二维软件编制,如图4所示。二维RPS编制繁琐,设计周期长。三维RPS设计,采用三维软件直接在3D车身数模中设计,RPS点A基准(定位面)采用白点标识、B基准(主定位孔)采用红色圆标识、C基准(辅定位孔)采用绿色圆标识,如图5所示,某车型侧围外板3D版RPS图。
车身夹具MCP设计
车身RPS设计完成后,夹具MCP按照RPS系统开始设计,夹具MCP必须与RPS点保持一致。考虑焊接操作空间、摆放姿态、精度控制及性能要求等问题,可适当增加MCP布置点, MCP定位面可在RPS同一基准面上进行适当调整(±25mm以内),不可切换定位型面,且必须保证前后工序定位基准统一。
传统的夹具MCP主要由三部分组成:定位夹紧位置布局图、夹紧定位说明表和MCS(夹紧定位断面图)。二维夹具MCP设计,使用二维软件,设计周期长,且在评审中需要打开三维软件,结合3D车身零件数模确认评审,工作效率低,问题无法有效识别。三维夹具MCP,使用三维软件直接在3D车身数据中进行设计,设计简单,更直观地显示了夹具定位、夹紧机构、操作空间等,更能验证RPS定义的合理性,有效地规避了实际夹具设计、生产等过程中出点的基准不合理的问题,保证了模具、夹具、检具基准的一致性及继承性,提高车身制造精度。具体设计形式如图6所示。
结语
随着汽车行业的发展,新车型车身RPS、MCP设计已基本趋于成熟,提升了车身制造质量水平,及新车型在市场上的竞争力。三维RPS、MCP设计形式,缩短了设计周期,提升了工作开展效率,但是三维RPS、MCP设计还不成熟,需要在新车型开发中不断地验证、总结,以弥补不足之处。
参考文献
[1] 赵彤.车身零部件基准点系统(RPS)研究[D].吉林:吉林大学,2007.
[2] 王艳.白车身拼焊夹具MCP设计方法[J].现代零部件,2012(3).
[3] 陈晓华,等.RPS在车身精度设计上的应用[J].汽车技术,2006(8).
[4] 李盛良,等.浅谈车身零部件RPS的设计[J]. 汽车工艺师,2017(1).
田飞,周海波,臧永志
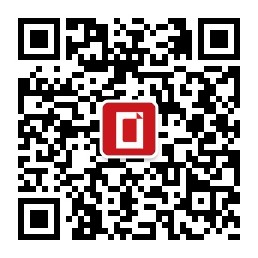