利用模腔压力控制增加工艺的稳定性
- 来源:国际塑料商情 smarty:if $article.tag?>
- 关键字:产品质量,塑料加工,因素 smarty:/if?>
- 发布时间:2021-04-14 10:38
产品质量是塑料加工公司重要的竞争因素之一。模制品的质量特性(例如:尺寸精度、重量和表面)取决于成型期间模腔中的热力学熔体状态。熔体状态通过其压力、比容和温度进行描述。对于高精度模制品而言,模腔中的可再现压力和温度曲线至关重要。
尽管机器设置参数不变,但是注塑成型工艺不可避免地会受到干扰,例如:不同批次的物料加工、物料条件波动或止回阀的关闭方式不同,都会导致熔体状态变化以及部件质量波动。因此,目前先进的控制系统已能使工艺适应主要条件并显著增加工艺稳定性。
一些系统通过注射压力的变化来检测粘度的波动,然后调整切换点和保压水平。但是,这些概念都无法检测出模具内部的干扰,例如:模具温度的波动和热流道表面的废料,它们都会改变流动特性。另一种方法是通过塑化系统的螺杆运动直接调节模腔压力。但是,系统行为和材料特性取决于许多因素,因此导致控制系统极其复杂。这些方法要求工作人员在安装控制系统时具备专业知识,而这在生产过程中通常是无法实现的。
在浇口处直接控制模腔压力
此外,这些概念不能调节熔体流到多腔模具的不同模腔中。这对异型腔模具尤为不利,因为其模腔的体积各不相同。为了确保每个腔体都具有高品质,浇口系统根据特定的工艺设置经过了精心的平衡和优化。因此,其平衡取决于工作点,因为干扰产生的工艺偏差会导致模腔的填充量发生变化。
因此,一种利用热流道中附加的阀门独立地控制每个模腔的熔体流动的系统被开发了出来。根据阀门位置的不同,将不同数量的材料注入不同的模腔中。但是,该系统不直接控制模腔压力而是控制浇口系统。此时的压力不能直接反映模制品内部的状况。
IKV 开发了一种新的控制概念,可直接在模具中调节模腔压力。该工艺通过热流道阀针的运动来控制传向模腔的压力。阀针的阀门行程越小,热流道中的压力损失越大,因为热流道中的横截面变小了。
阀门行程越小 模腔内压力水平越低
在控制概念开发的初步测试(表 1)过程中,首先对阀门行程与模腔压力之间的关系进行了量化。一种用于电动注塑机的模具被用于这些实验,该模具的腔体具有自行车鞍座的几何形状(标题图)。
两个组合式 p/T 传感器沿着流道被安装在浇口附近和填充末端(填充量分别 22% 和 98%)(图 1)。模具配备了带有伺服电动阀浇口喷嘴的热流道。由 cRIO 系统控制的热流道阀针在注射阶段开始之前完全打开(最大阀门行程:18mm)并在保压阶段设定了不同的阀门行程。
初步测试还分析了在保压阶段恒定的阀门行程对模腔压力的影响。在保压阶段,当阀针的阀门行程为 18 mm 时,模腔内测得的压力约为 115 bar(图 2)。将阀门行程减少到 5 mm 时,压力水平与参考曲线(阀门行程 18mm)相比降低了 10 bar。通过对比不同阀针位置的压力曲线可以确定,阀门行程越小,模腔内的压力水平越低。
较低的压力水平是由于较小的阀门行程导致横截面积减少引起的。阀门行程对模腔压力的影响随着行程的减小而增加。例如:阀门行程在保压期间每小 1mm,模腔压力曲线与参考值(阀门行程 18mm)相比就小约 0.5 bar。但是,热流道行程每增加 4mm 不到,压力损失就会显著增加,从而导致模腔内部压力下降。阀门行程在 0-4mm 之间时,横截面产生了变化,因为针尖会引起横截面缩小并导致热流道关闭。因此,热流道中的压力阻力达到最大(图 3)。当阀针的阀门行程较大时,热流道中的压力阻力随着热流道中的环流长度而变化。但是,流动长度对压力阻力的影响小于热流道横截面变化的影响。
此外,在浇口附近测得的压力曲线中,密封点的压力明显增加。追其根源,因为部件包紧了压力传感器,然后压力传感器伸出了模腔表面。
阀针关闭:每个定位阶段压力略有增加
在后续测试过程中,热流道阀针不仅在保压阶段保持着规定的阀门行程,而且还根据预设的位置曲线进行了移动。因此,他们还对热流道逐渐关闭对模腔压力的影响进行了研究(图 4)。阀门行程经过六次 3mm 步进从 18mm 减少到了 0mm。每个阶段保持 5 秒。
最后产生的模腔压力略低于参考曲线(18mm)。与不变的阀针位置和热流道中较高的压力阻力相比,热流道中较长的环流导致了偏差。但是,阀针运动开始时,压力将增大。原因之一可能是由于阀针的闭合运动导致了熔体受到额外的压缩,并且更多的熔体被注入膜腔中。
阀针开启:每个行程阶段压力略有降低
最 后, 对 阀 针 在 保 压 阶 段 的 反 向运动进行了分析。在热流道逐步打开的过程中,阀针在注射阶段在阀门行程达到 18 mm 后 完 全 关 闭, 然 后 经 过 六 次 3mm 步进从 0mm 开启到 18mm。同样,每个阶段保持 5 秒。到达切换点之后不久,测得最大模腔压力超过了 115 bar,该值与其他测试相比更高(图 5)。
与阀针逐步关闭期间出现的轻微压力峰相似,这也是因为阀针横向移动导致熔体受到额外压缩而引起的。热流道完全闭合中断了从塑化单元到模腔的压力传递。因为熔体冷却收缩,并且由于模腔封闭而无法被补偿,模腔压力降低了约 50 bar。热流道逐步打开时,在模腔中测得的压力再次上升到与流道系统在整个保压阶段完全开启时几乎相同的水平,因为熔体流动可对收缩进行补偿。
与之前讨论的实验相反,在阀针运动开始时,每个阶段都会短暂地出现小幅压力下降。与之前的测试点相反,熔体因为阀门的开启运动而被减压。
填充末端的传感器还可以检测阀针运动对测得的压力曲线的影响。此时,当热流道从注射阶段切换到保压阶段后关闭时,压力曲线也出现降低的现象,它基本也可以通过逐步开启进行补偿。但是,在阀针运动开始时,远离浇口处的压力下降并没有那么重要。
究其原因是熔体温度较低,而这会导致塑料更快固化并降低熔体中的压力传递。此外,传感器位置和浇口之间的距离越远,产生的影响就越小。
根据不同研究的结果,后续研究开发了一种控制策略,该策略将热流道阀针用作专门控制模腔压力的调节变量。通过该控制系统获得的结果见项目的总结报告。未来,利用热流道阀针控制模腔压力的方法将被用在异型腔模具中,因为这样可以对工艺条件产生模腔特定的影响。
结语
测试表明,不同的模腔压力可通过在保压阶段移动热流道阀针来实现,无论是在浇口附近还是填充末端。因此,热流道阀针可被用作控制注塑工艺的调节变量。模腔的压力水平与阀针的阀门行程有关,但是压力损失只能通过改变喷嘴处热流道的流动横截面来产生显著影响。另一方面,改变环流的长度仅能略微影响传递到模腔中的压力。
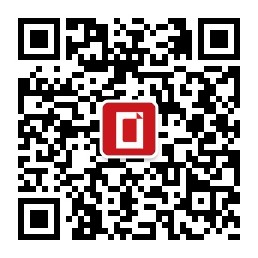