汽车发动机总成的降本增效之道
- 来源:国际汽车设计及制造 smarty:if $article.tag?>
- 关键字:汽车,发动机,增效之道 smarty:/if?>
- 发布时间:2022-03-04 19:05
近几年,随着新能源汽车的崛起,其技术不断发展让制造成本得以降低,传统汽车面临着巨大的竞争压力。同时,伴随着各种外部因素的不确定性,为了抵抗风险,企业的降本增效势在必行。
“在汽车发动机制造过程中,企业要想实现降本增效的目标,就必须选择适宜的技术,同时减少投资,以较低的制造成本生产,从而提高企业的整体综合竞争力。根据国际汽车行业经验,产品设计直接影响今后生产约70%的制造成本。因此在产品研发阶段对其方案审核及工艺技术分析,可以及早发现问题并有效降低制造成本和新增投资。”东风汽车集团有限公司原科技工程部、机加首席工程师曾凯红分享道。
汽车产业是武汉当地的支柱型产业,仅在武汉的经济技术开发区内,聚集了7家汽车整车企业、12个汽车总装工厂、500多家汽车零部件企业。近日,东风汽车公布了今年1月的销量情况,汽车销售达34.17万辆,同比增长6.1%,实现了新年开门红。本期会客室,让我们走进武汉的东风汽车集团,看看其在机加车间的降本增效方面遇到哪些难题,正在进行哪些工作,又有哪些实例分享。
技术策略为攻,引领企业实现目标
整车与发动机项目生产准备是企业工作的基础,对投入产出水平、制造成本高低、经济效益大小起到关键作用;制造技术工作是将产品技术、工艺技术、装备技术、材料技术及管理技术转化为生产力中心环节和扭带。然而,由于客户对加工产品的品质和交期要求越来越高,机械加工所涉及生产要素多而流程复杂,造成制造成本难以控制。同时出现产品的质量问题难以在短期找到真正原因,解决时间偏长而且可追溯性差,增加了质量成本。
对此,曾凯红从产品结构性技术分析、制造技术方案、同步工程、商品化流程等方面带来东风汽车在降本增效方面的技术策略分享。
从产品结构性技术分析来看,需要从制造的观点来分析方案的合理性,以及其标准化和系列化的程度、产品的继承性、选材是否合理等因素都要考虑在内。主要的对策集中在优化产品结构,保证其尺寸与精度,改进产品设计和加工方法,选择合适的原材料。
从制造技术方案来看,要结合企业现状、资源匹配度以及工艺发展趋势,涉及到产品结构特点、产品种类及复杂程度、产量、生产方式、发展前景、人员设备等多种因素,企业需要根据自身的情况来综合考虑。
同步工程也叫并行工程,描述的是产品的研发团队,涉及到整个制造环节的技术人员、采购等项目团队,在产品概念设计初期需要进行同步交流和工作,以保证新品开发周期和开发质量,降低产品研发和商业化过程中的制造技术风险。同时,供应商在早期设计阶段也会参与到开发过程中。此外,对于开发过程的关键问题进行评估可以提高产品设计的可靠性,改善制造工艺,降低制造投资和成本。
“通过精细的设计与制造并采用同步工程,可以提高研发和制造环节技术之间的协作水平,尤其是隐性知识及经验共享,从设计环节开始就彻底地审视产品构造和零件形态,进行与产品开发有关的技术改进及优化。这样就可以避免因简单粗暴的削减成本后而导致产品品质的下降,又可以从源头保证品质避免后期频繁进行设计变更而造成人力、物力等资源浪费。”曾凯红如是总结道。
启发借鉴,看发动机总成降本增效实例
除了对东风汽车降本增效的技术策略进行了分享,曾凯红还分享了其策略在四缸柴油机缸体、中型柴油机四六缸的平台化设计等方面的应用实例。
曾凯红举了一个四缸柴油机的缸体结构优化的案例。“研发部门在设计之初考虑使用干式缸套,但由于其接触面积大,压装的时候变形非常大。但如果采用湿式缸套,四缸柴油机轴向尺寸会加长,因此也不合适。最后决定的是采用本体,用铸造添加活性元素以满足发动机的性能要求。”曾凯红说道,“因为取消了干式缸套,缸体的成本减少了。此外,由于干式缸套需要精加工,取消干式缸套可以减少精加工设备的投资,整体来说实现了降本增效。”
此外,他还举了一个中型柴油机四六缸的平台化设计的例子。“缸体后端的位置是燃油泵,由于四六缸的燃油泵安装尺寸是不一样的,设计师在最初考虑的时候两者的坐标尺寸是不统一的,这就使得柴油机缸体整个曲轴和燃油泵要用专用设备加工才能保持其精度的一致性。而四六缸两套产品结构则需要工厂对产线进行双倍的投资,成本较高。最后,通过和研发部门的沟通协调,将坐标尺寸进行统一,节省了投资成本。”
除了对产品结构及平台进行优化,汽车发动机零部件的加工工艺也在向柔性化、集成化、模块化的方向发展。“对于缸体和缸盖的加工,我们会将精加工和粗加工分成不同的生产单元。传统串联式的生产线当一台设备出现故障,整个生产线都会受到影响。而集成化的设备模块没有这样的担忧,提高了加工效率,对于扩产的灵活性有很大的帮助,这也帮助企业从另一个侧面实现降本增效。”
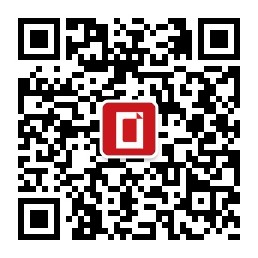