机器人焊接,如此高效
- 来源:国际金属加工商情 smarty:if $article.tag?>
- 关键字:机器人,焊接,高效 smarty:/if?>
- 发布时间:2022-06-15 17:01
2017年底,总部位于美国田纳西州迪克森郡的Truform制造公司,安装了1台660吨的Stamtec机械冲压机,以承担其来自汽车领域的新订单。随后不久,这家公司又安装了两台Stamtec冲压机(一台660吨位,另一台330吨位),以实现额外的冲压作业,以确保其汽车及电器领域的客户能及时收到所需的零部件。
“我们重视这里的每件设备,都做了应急备份,”Truform副总裁Paul Beaton说,“在新冠肺炎疫情期间,我们始终没出现任何类型的客户服务中断,保持了百分百准时发货。这都要归功于我们设备的可靠性和互换性。”
Truform公司总经理Mart Rowe表示,借鉴冲压部门所实现的兼容性和互换性,Truform也已开始在焊接操作领域采取同样做法,增加了12台ABB FlexArc机器人熔化极气体保护焊(GMAW)单元。
2003年Truform公司安装了第一台FlexArc单元,并在2017年底和2018年用8台单元替代了最初的加工单元和手工焊接设备,以满足来自汽车合同的大量零件订单;2020年公司又增加了4台加工单元。
新增的机器人焊接设备,标志着Truform公司在规模和产品组合领域的进步。这家公司成立于1999年,占地20000平方英尺,拥有2台200吨位的冲压机。2012年被西斯勒制造集团(Sisler Manufacturing Group)收购后,公司开始增产。在家电行业有丰富经验的2位企业家Jon Sisler和Brett Sisler,将Truform从一家百分百为汽车领域供货的企业,转变为一半在电器领域,一半在汽车领域,厂房也达到了近10万平方英尺。公司的生产能力也在增长,有大约175名员工分两班工作,负责级进模冲压、焊接和组装。公司在2017-18年度安装的多台冲压机,足以支持新型汽车加工作业,是其汽车业务提高到占比70%的关键。
在一张今日生产快照上,可以看到这家公司的进一步增长势头:Truform公司在其占地13.7万平方公里的两幢紧邻的厂区内,生产40%的汽车以及40%的电器产品。Beaton介绍说,剩下的20%将用于新项目——酒店餐饮服务设备和泳池设备的制造。Truform公司在电器铰链等产品的组装业务和生产线上投入了大量资金,还组建了一个全是AMANDA设备的制造车间,满是钣金光纤激光切割机和冲床。
他说:“这个新项目涉及大量的泳池加热器、熏炉、煎锅和炸锅。”他列出的只是公司新的制造、组装业务所生产的终端产品的部分零部件。“它使我们能够规避像过山车一样起伏不定的汽车供应链风险。我们的增长主要来自新的制造业务,我们将再次增产,以应对商用电器订单的增加。”
独特的加工单元
让我们重回机器人焊接这个话题。Truform使用机器人焊接设备来满足汽车需求。在每台FlexArc机器人焊接单元中,ABB机器人与米勒电机公司的焊接控制器交相互联。这种单元可以将各家供应商设备联结起来协同作业。
“在过去几年里,我们也尝试过其他方法,”Beaton说,“但ABB+米勒的组合取得了最好效果。”
Truform公司增置的大量焊接单元,明显提高了生产率,同时也提高了单元的独特性。例如,FlexArc配置允许操作员在机器人焊接单元时在另一侧装卸组件。还有一个助力生产力提高的因素,被Beaton称之为“靶心”。
“这个功能会计算工具的中心点,”他解释说,“当有人对单元进行预防性维护,比如更换焊接喷头或接管时,焊接端点可能会改变。但在使用智能靶心程序之后,机器人就会计算出正确的中心点,正确运行加工作业,无需重新矫正。这是一项关键性功能。”
这些功能有助于更多加工作业的完成。当加工单元中有众多作业在运行,拥有可以从一项任务有效切换到下一项任务的能力,就变得至关重要了。
“所以我们设置了机器人焊接单元,可以像冲压机那样可以快速切换。”Beaton说。为此Truform公司还为每项加工作业设计了定制焊接夹具,可以快速连接或断开这些电气、气动连接装置。
他解释说:“一旦我们从夹具托板处插上这些连接,机器人控制系统就知道该调用哪个焊接程序。”
而且每台机器人焊接单元都可以兼容任何夹具。“机器人上可以安装任一种夹具,”Truform公司制造经理Jody Crumpton说,“我们不会让每台机器人运行所有加工任务,但是一旦出现新增任务或意外情况,我们是有能力应对的。”
在平台和Truform公司的交叉培训下,车间的操作人员们也具有灵活的应变能力。
Beaton表示:“我们的员工有能力操作公司14台机器人焊接单元中的任意一台(ABB公司出品的12台,以及其他2台,分别来自OTC Daihen公司和Yaskawa Motoman公司)。这些机器人焊接单元配有通用的控制系统和工具平台。而且为防止受到新冠肺炎疫情影响,公司团队还特地接受了商业电器运营和组装业务的交叉培训。”
因为操作人员和工具平台可以在任一台机器人上操作或运行,所以Truform公司倾向于将其机器人焊接作业根据所需焊丝的类型和大小分成不同区域,将40%的机器人单元用于焊接低碳钢制造的汽车转向系统系列,60%的机器人单元用于焊接不锈钢制造的排气系统零件。
将焦点集中在防错
在Truform公司冲压的零件数量庞大,充分满足了这些机器人焊接单元的加工好“胃口”。而这些焊接单元的防错机制,是有助于确保整个焊接作业质量的。
“防错机制对我们来说非常重要,”Beaton说,“我们正在努力将防错机制尽可能多地加入焊接工具中,以实现过程中检验。焊接产生的热量有时会使传感器失效,那时我们会使用视觉系统,效果很好。”
内部集成能力
据Beaton和Crumpton介绍,Truform公司设置了一间全面储备工具室,配置了经验丰富的工具设计师和架构师,可以根据产能和工作流程,在公司内部制造出大部分的焊接夹具。
Beaton说:“我们的工具设计师能够应用3D CAD程序进行夹具设计,在机械车间使用我们的线切割机、数控铣床以及传统的数控机床将它们制造出来,再用公司内部的三坐标测量机进行全方位检验。之后,控制工程师们可以连接界面,指引机器人应用新夹具。”
Truform公司常将新的焊接夹具与机器人集成起来。这些机器人单元最初都是“交钥匙”安装完备的,本身已集成了GMAW设置和电源。
InMotion公司是ABB公司的系统集成合作伙伴,负责支持Truform公司焊接单元的设计、安装和运行,最早提供服务的时间可以追溯到2003年。除了在焊接夹具上协助Truform外,InMotion公司还负责焊接单元的布线连接和焊接编程。
InMotion公司合伙人Bryan Brewer回忆说:“设计所有夹具并配置快速更换能力,是我们面临的主要挑战。每个夹具都涉及不同数量、类型的传感器、开关和阀门。在焊接单元中,当从一个夹具切换到另一个夹具时,必须确保一切运行良好。”
除控制系统之外,Truform还投入了大量资金,以确保一切都能协同工作——通过冲压、焊接、制造、组装等操作,保证材料和零部件顺利流经各项工序,通过过程中检验,按时出厂。
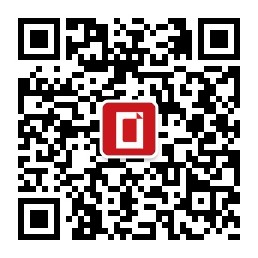