中远川崎:“智造”船舶 由浅滩驶向深海
- 来源:中国信息化周报 smarty:if $article.tag?>
- 关键字:船舶,中远川崎,智能制造系统 smarty:/if?>
- 发布时间:2016-01-19 11:51
在南通中远川崎船舶工程有限公司(以下简称“中远川崎”)的制造车间内的3条机器人自动化生产线上,机器人不停地挥舞着灵巧的臂膀忙碌地作业。以前,中远川崎钢板的划线和切割两道工序都需靠人工来完成,不仅工时长,而且劳动强度大。眼下,只需一位工人轻击鼠标发布“命令”便可由机器人来完成。如今,这种高效率、低强度的生产作业模式已经成为中远川崎制造车间内的“新常态”。
随着全球化的快速发展,国家之间的经济往来变得日益密切。作为大宗货物的主要运输工具——船舶所扮演的角色以及所发挥的作用也就越来越重要。作用的提升,随之而来的就是要求和标准的增多。这也就意味着生产设施必须变得更加灵活,才能够快速地响应市场变化。
面对波诡云谲的市场环境,韩国、日本等发达国家已经抢先一步进入智能造船领域。然而,起步较晚的中国造船企业也已经快步迈入这一领域,中远川崎就是其中优秀的代表,并由此入选了工业和信息化部智能制造试点示范项目。
信息化建设贯穿始终
从2007年开始,中远川崎就大规模利用信息技术改造传统设计建造手段,升级改造计算机集成制造系统功能,进一步提升信息系统的应用范围和信息系统集成度,并扩大数字化制造装备的使用规模,实现了以信息化和工业化深度融合为标志的数字化造船。
经过几年的开发、创新和实践,建立了完善的计算机集成制造系统,将贯穿船舶产品全生命周期的CAD、CAPP、CAM、ERP等高度集成应用,在研发、设计、采购、制造、财务、管理等流程中实现信息化和数据共享。
2012年,中远川崎确立了将智能造船作为转型升级的主攻方向和实现造船强厂的主要途径,相继投产4条机器人生产线。通过不断技术攻关,初步建立了以数字化、模型化、自动化、可视化、集成化为特征的智能造船和精益管理体系,真正实现了研发、设计、生产、管理等环节全面融合、协同运行,已建成具有示范作用的船舶制造智能车间,实现了各加工系列的智能制造,达到工装自动化、工艺流水化、控制智能化、管理精益化,保障了产品质量的稳定,缩短了加工周期,极大地提高了生产效率,产品质量和建造效率达到世界先进水平。
之前,中远川崎制造车间内型材班组人数最多时有36人,引进自动化生产线后,人员缩减了一半。同时,钢材的划线和切割全部由机器人完成,工人只需用电脑确认操作和在旁边查看就行,1个人可以完成6个人的工作量。而且,原来切割一个分段所需钢材需要3天,现在半天就可以完成,每天可切割完成160~170根角钢。此外,所有型材、条材的切割尺寸、标准等信息都由企业设计部设计、修正后,输入信息系统;联网的自动化生产线依照规格进行分料、切割、运输等,确保了产品品质的精准性与稳定性。通过近4年的应用,南通中远川崎的大部分车间已经实现自动化操作,钢板一次性利用率达92%,反复利用率超过95%,3条自动化生产线让相应工序的生产效率提高了约七成。
全景展现智能制造系统
中远川崎高度自动化的流水作业生产线加上柔性化的船舶生产工艺流程,实现了船舶制造的自动化操作和流水式作业。同时,将反映生产状态的各类信息集中和融合,为操作人员提供一个直观的加工场景,确保准确掌握信息,实现快速作业。
型钢生产线。型钢是船体常用部材之一,原先的生产方式,从画线、写字到切割、分料,完全采用手工作业,效率低,周期长,劳动强度大,且难免出现误操作。型钢自动化生产线建成后,实现了从进料→切割→自动分拣→成材分类叠放全过程的智能制造,包括物料信息传输和物料切割智能化以及物料分类感知智能化,有效减少了人工成本,缩短了生产周期,降低了劳动强度,为后续扩大机器人应用积累了经验。
条材机器人生产线。条材是分段制造的主要部材之一,它的特点是数量多,大部分部材比较短小。原来的生产方式,包括画线、写字、开条、端部切割、打磨、分料等全是手工作业,效率低,生产周期长,容易出错。条材机器人生产线的投产,实现了信息传输和物料传输感知智能化以及加工智能化,提高了生产效率,缩短了生产周期,降低了劳动强度。
先行小组立机器人生产线。尽管造船中厚板电弧焊接实现机器人作业困难很多,但中远川崎还是从最简单的先行小组材开始,推进机器人焊接。传统的制造方式中,钢板在定盘上全面铺开,一块一块地装配、焊接、翻身、背烧,占用面积大,制造周期长,效率低。先行小组立机器人生产线投产后,实现了工件传输和焊接智能化,以及自动背烧、自动工件出料,整条生产线仅配一名员工操作,配员减少一半以上。
流水线生产方式是工业化大生产的必然要求。对造船业而言,车间内生产作业的流水线化将是今后实施船舶智能制造的一个重要发展方向。目前中远川崎已实施了大舱肋骨生产线、Y龙筋生产线、焊接装置等数个半自动化生产线技改项目,取得了良好的效果。
小组立机器人焊接生产线。全线长84米,包括四台焊接机器人,以焊接散货轮N分段为主,较3号先行小组立生产线更为先进。采用三维模拟部材,利用专用KCONG软件进行自动化生产。四台机器人能够单独焊接,也能互相配合作业,可以针对部材大小,灵活应对各种情况。整条线只需要2~3人就能正常运转。
智能物流系统。采用“横向到边、纵向到底”的设计原则,建立了功能完善的智能物流系统,并与设计系统高度集成,从而将企业的人力、资金、信息、物料、设备、时间、方法等各方面资源充分调配和平衡,为企业加强财务管理、提高资金运营水平、减少库存、提高生产效率、降低成本等提供强有力的支持。
中远川崎的智能造船模式使设计、制造、加工、管理信息实现了一体化操作,贯穿了零件设计信息、工艺信息、工装信息、材料配套信息、加工信息和装配信息的生成和传输全过程,并且在采购申请单、物料清单、托盘清单等业务方面全面实现了无纸化。
另外,机器人作为开启下一代技术革命的关键,给传统行业特别是传统制造业中的造船业带来了巨大挑战和无限的想象空间。船舶产品的非标准化和定制化特点,虽然给船企应用机器人进行生产带来了一定的困难,但经过多年的发展,机器人参与造船并助力造船业发展已经成为现实。
相关链接
随着社会和技术的不断发展,信息化已成为造船生产不可或缺的管理工具,造船业传统的生产及商业模式正逐渐被信息化、网络化、智能化等现代造船模式所取代,国内船舶及海工企业须抢抓机遇,不断深入完善信息化建设,加快实施“数字化造船”步伐,促使船企在双高船、海工核心装备等一些关键领域抢占先机、取得突破,实现中国制造向“中国智造”转型。中远川崎作为船舶行业首个上榜智能制造的项目,为传统制造业的船企生产车间赋予了新的意义。
本报记者 路沙
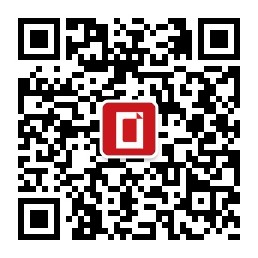