实践智能制造
- 来源:中国信息化周报 smarty:if $article.tag?>
- 关键字: smarty:/if?>
- 发布时间:2018-05-24 10:26
习总书记强调,振兴制造业特别是先进制造业,短期看是实现经济良性循环的关键,长期看是国家经济命脉。要将发展先进制造业作为长期坚持的战略任务,以供给侧结构性改革为主线,以实施“中国制造2025”为抓手,强化创新驱动、改革推动、融合带动,推动质量变革、效率变革、动力变革,加快实现我国制造业由高速增长向高质量发展的跨越。智能制造是发展先进制造业、培育全球经济发展新动能的关键,也是中国实现新兴产业培育发展与传统产业改造升级有机结合的最佳途径。“中国制造2025”已将智能制造作为主攻方向和突破口。抓住智能制造这个核心,必将对深化制造业和互联网融合发展,夯实实体经济根基产生重要而深远的影响。质量变革、效率变革、动力变革是加快发展先进制造业的根本要求。面对历史机遇,我们必须顺势而为、前瞻部署,加强战略谋划和统筹协调,推动互联网、大数据、人工智能和制造业深度融合,促进先进制造业快速健康发展。总体来看,通过各方共同努力,推进智能制造的社会共识已经形成,成效不断显现。同时我们也要清醒地认识到,推进智能制造是一项复杂的系统工程,需要逐步推进落实。不过让人欣慰的是,越来越多的智能制造实践正展现在我们眼前。
案例1
海尔大规模定制实践
海尔集团是中国智能家居产业联盟的发起者和参与标准制定者。智能家居要“落地”,实现大规模应用,必须摒弃传统的制造模式,以互联网思维进行变革和创新,通过技术手段与用户的个性化需求紧密对接,带来最佳的用户体验。海尔智能研究院与菲尼克斯电气联合研制大规模定制最佳实践设计方案,凝结了海尔集团对未来家电智能制造的理念和菲尼克斯电气的智能智造观。
海尔大规模定制实践项目是采用菲尼克斯电气的智能化、模块化的设计理念,展示家电产品从云端下单的个性化定制、智能组装、智能测试、个性化打印、智能包装,到智能物流的生产制造产业链的全过程。该项目基于菲尼克斯电气对工业4.0及智能制造的深刻理解,将机器人、AGV、3D仿真技术、MES、ERP等智能生态共存元素与海尔COSMOPlat智能制造云平台无缝连接,体现了智能制造的魅力。海尔COSMOPlat平台作为整个系统的管理核心,通过移动终端的交互操作,就可在众创汇平台上进行产品设计,通过COSMOPlat云平台接受用户订单信息。云平台收到订单信息后将生产信息指令下达给生产控制系统PLC,生产控制系统PLC控制机器人自动抓取物料,产品自动装配、自动打印个性化信息和自动包装,AGV自动执行插单功能,65英寸大屏幕看板上实时显示智能制造的所有过程和生产数据。三维仿真既可以离线仿真所有生产流程,也可实时显示现场设备的运行状态和订单信息。从下单到产品交付,只需要短短三分钟。整个过程透明、高效、智能,实现了由菲尼克斯电气提出的生产制造自动化、流程管理数字化、信息管理网络化和智能制造云端化四步曲的智能生态智造观。
首先,海尔大规模定制实践项目最大限度地利用智能设备实现生产制造自动化。机器人、AGV等智能化产品在COSMOPlat与PLC全面信息交互的前提下,由PLC控制,完成了产品的生产过程,显著地降低了生产过程的人力成本,由项目实施前的8人减少为1人,为实施前的12.5%,操作工与机器人的参与比达到了1:6,人机占比领先于行业平均水平。智能设备的大量运用也促进了产品质量的提高,不良品率降至0.8%。
其次,海尔大规模定制实践项目全面实现了流程管理数字化。合理布置的传感器所获取的生产过程数据与设备状态,由PLC实时通过生产区域内的工控机、大屏幕看板以及生产区域外的计算机,数字化、图形化地友好呈现给操作人员与管理层,改变了以往的数据展示方式,解决了生产数据的实时性问题,也降低了原材料的库存率,缩短了生产环节的待机时间,运营成本降低了20%,具有技术引领的意义。
再次,海尔大规模定制实践项目全面实现信息管理网络化。借助菲尼克斯电气提供的基于以太网的工业4.0PROFINET主干网、工业智能交换机、无线接入设备以及信息安全设备,项目实现了从现场执行器层到公司管理层之间数据流的无缝连接,采用“一网到底”,极大地节省了项目实施前因不同协议而产生的硬件投入,同时,可靠的信息安全解决方案也为智能工厂的安全运行提供了坚实保障。网络的灵活运用改变了人工抄录数据的旧方式,极大地提高了数据的时效性,保证了生产的连续性,企业生产效率提升20%。
最后,海尔COSMOPlat平台以极其友好的形式将制造过程呈现在了云端,全面、开放地将定制化的家电产品以生命周期的形式呈现给用户,实现用户全生命周期与企业零距离互联互通,创造用户最佳体验。用户与项目环节的全面交互体现了工业4.0对用户交互参与的要求,打通了从供应链到生产链、管理链和服务链的全过程。以资源共享的形式对生产方式产生了根本性的变革,企业资源重复利用率提高4%。
案例2
上海宝钢 基于云实现虚拟远程运维
“中国制造2025”对设备管理与维护赋予了新的内涵,宝钢技术定位于设备全生命周期智慧服务的供应商,远程运维将是宝钢技术智慧服务的重点发展方向。宝钢技术与西门子决定成立“基于云技术的虚拟远程运维平台及标准研究”项目组,共同研究设备运维在智能制造背景下的未来蓝图与实施路径。同时在流程型行业和离散型行业寻找符合虚拟远程运维特征的落地项目,研发虚拟远程运维平台和标准核心技术。基于云平台的运程运维App的开发,基于运维平台虚拟集控管理的数字化工具开发,基于运维数据的大数据分析等,面对智能制造,形成设备运维方面智能制造的人才,积累实施经验,在全行业内复制推广,远期共同进行商业开发。
项目通过对设备虚拟远程运维平台及标准的研究,形成比较完善的虚拟远程运维平台,实现生产线设备状态监测、数据分析诊断、状态预测、关键部件全生命周期分析、数字化可视化展示等功能,并固化形成5项标准,将原有设备运维的“预防维修模式”转变为更先进的“预知维修模式”,甚至是预测维修模式,是全行业设备管理方面一个跨越式的发展。
国外先进制造企业,如日本新日铁,已经采用了先进的监测诊断技术来掌握生产线的设备状态,并以设备状态结果来指导设备运维过程,但尚未形成标准。目前国内尚未有虚拟远程运维平台,基本处于预防性维修或事后维修的阶段,属于比较传统的设备运维模式。国内某些企业,如宝钢股份目前采用的是以预知维修为基础的预防维修模式,其运维模式代表了国内先进水平,但与远程运维的要求相比还是有一定的差距,还处于常规运维发展的高级阶段。远程运维需要打破原有的设备管理界限,将原有的“预防维修模式”转变为更先进的“预知维修模式”,甚至是预测维修模式,是全行业设备管理方面一个跨越式的发展。
远程运维与目前采用的常规运维相比,无论是掌握状态信息的全面性、状态诊断的准确性、设备的可靠性、设备维护的经济性、产品质量的稳定性各方面均有质的变化,是设备运维的发展方向,具有很好的先进性。
通过该项目研究,将形成比较完善的虚拟远程运维平台,实现生产线设备状态监测、数据分析诊断、状态预测、关键部件全生命周期分析等功能,并固化形成标准,实施后将达到目前国际先进的设备运维水平。预期达到设备故障降低30%,设备维修量降低20%,取得巨大的经济、社会效益。
我国是制造大国,制造产线多,尤其是大型连续的产线,具有设备精度高、复杂程度高、运维难度大等特点,包括控制系统、动力系统和传动系统三大共性系统以及部分个性化系统,研究设备系统的虚拟远程运维平台及标准对于流程型行业和离散型行业均具有非凡的意义。通过搭建数据云平台,选取合适的设备关键表征参数、研究数据接口规范、研究设备状态诊断模型,研究设备虚拟化、可视化展示,形成设备全生命周期运维管理的规范,整个虚拟远程运维的平台及标准可以非常容易地适用于全行业的设备运维管理,随着标准在全行业的推广应用可快速提升我国设备整体运维水平,具有极高的推广价值。虚拟远程运维平台所采用的技术具有广泛的可移植性。其应用的云平台、大数据预警、网络安全防护等新型技术更是能在传统制造业的产业升级改造中发挥示范应用的作用,有助于我国工业整体能力的快速提升。
案例3
一汽-大众动力总成试点智能工厂
一汽-大众汽车有限公司是由中国第一汽车股份有限公司、德国大众汽车股份公司、奥迪汽车股份公司和大众汽车(中国)投资有限公司合资经营的大型乘用车企业。一汽-大众动力总成智能工厂项目,通过四个维度建设特色的智能制造样板工厂:
1.先进物联网技术:利用无线传感技术、RFID技术,解决异构系统、设备、网络互联,实现信息物理网建设。
2.系统集成和生产管理:以SOA为核心,以ESB为手段,实现“合纵连横”的信息系统一体化集成。信息能够贯穿于工艺规划、制造、质量、物流等环节,实现产品的全生命周期管理。
3.大数据和云计算:通过大数据获取、挖掘、分析,实现基于大数据驱动的企业管理的综合评估体系,通过“图形化展示”“钻取式查询”“透视性分析”,实现对指标的逐层细化、深化分析。实时反映企业的运行状态,将采集的数据形象化、直观化、具体化。
4.统一的系统管理平台:利用远程监控技术、移动终端等设备,能够获取各类信息、联动各类报警,实现统一管理。
对于工厂智能化水平的量化考量,可以从六个维度进行:数据加工能力、机器间通信能力(M2M)、生产网络的集成度、信息和通信技术的集成度(ICT)、人机交互的水平、柔性化生产。
对于一汽-大众发传厂动力总成智能工厂项目,其实施前后的效果非常明显。
数据加工能力:目前发传厂生产过程中的生产数据仅存储一小部分,主要用于汇报或者文档存档。在项目实施后,可实现对生产、设备等过程数据的实时采集、存储与分析,可评估生产过程;大量的数据加工与分析可实现自动生产过程的设计和管控,并进行预测。
M2M:目前发传厂设备均具备总线接口和工业以太网接口,但是总线接口的应用仅仅局限于单台设备内部部件间的通信、装配线的前后工位的通信以及一小部分的设备间的集成,并未实现设备与设备之间的互联。在项目实施后,机器与机器间实现互联,可通过网络服务访问其他机器。上下工序之间的机器可以进行加工参数共享,实时对加工参数进行修正和补偿。通过MES与ERP的集成,机器可以直接和管理网络甚至互联网通信,实现设备的远程监控。
生产网络:目前发传厂的生产网络和办公网络脱节,生产网络产生的数据如产量、设备状态、工艺状态等等无法直接传送到办公网络,而是通过人工进行统计、录入、汇总后再通过电话和邮件的形式传送给办公网络。项目完成后,将实现生产网络和办公网络的集成,生产现场的各种数据可实时采集,生产网络和办公网络的数据交换有统一的数据格式和规则,通过预设的分析处理方法将有用的信息直接传递或推送给办公网络相关人员,从而便于快速分析和决策。
ICT:目前一汽大众供应商和客户等分别通过ERP集成在一起进行信息交换与业务沟通,而这些信息如生产计划的下达与生产车间的交换则以人工电话和邮件的形式进行通知。项目完成后将实现生产车间信息与管理通信技术的集成,将供应商和客户紧密的集成在生产过程中。
人机交互:目前发传厂的人机交互仅限于在生产现场通过操作面板进行。而项目实施后,设备与设备互联,设备与计算机互联,可实现远程的监控与控制,实现集中式的生产监控和控制,并可通过手机或Pad等移动终端作为人机交互界面,大大提高了人机交互的便捷性与交互效率。
柔性化:项目实施后可实现灵活的生产系统管理,实现不同型号的发动机快捷换线生产。
一汽-大众动力总成智能工厂以先进的自动化信息化生产设备、完善的康采恩生产管理体系、强大的市场份额为基础,依托于CPS物联网技术、MES制造企业生产过程执行系统、SAPERP企业资源计划,SAPHANA大数据云计算等全球先进技术而建立。
一汽-大众动力总成智能工厂项目在“生产制造”“产品检测与测试”“质量控制”“刀具管理”“物流管理”“物料管理”等全流程达到了智能装备全覆盖。机加生产线大规模使用工业机器人,配合自动输送料道等实现生产的全自动化;双主轴加工中心的大量使用,使生产线具备极高的柔性生产能力;大量采用超硬材料切削刀具,能够实现高速切削加工,实现高效率生产;部分生产线采用微量润滑、干式切削等先进切削方式,兼顾了规模化生产与环保需求;装配生产线应用有先进的集成质量控制系统,包括装配回转力矩检测、压装力与位移监控、在线试漏、在线冷试测量及全过程装配零件二维码记录等,实现装配过程质量的全面控制。
汽车发动机、变速箱等产品的高效加工装备、柔性装配装备以及试验检测装备等技术均属于“中国制造2025”的关键领域。动力总成智能工厂的成功打造,将为汽车行业,乃至其他行业建立一个样板工厂,其示范性和作用将是巨大的。
本报记者 霍娜
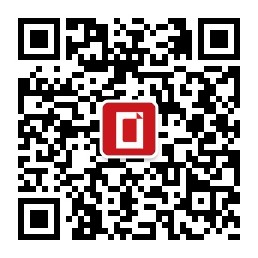