冶金自动化系统的优化研究
- 来源:消费电子 smarty:if $article.tag?>
- 关键字:生产调度,设备管理,能耗控制 smarty:/if?>
- 发布时间:2025-04-12 10:22
兰丽娟
【摘 要】冶金自动化系统是现代冶金工业流程控制的重要组成部分,对提高生产效率、降低能耗、确保产品质量具有重要意义。然而,当前的冶金自动化系统仍存在一些优化空间。本文研究了冶金自动化系统中的优化算法,探讨了其在生产调度、设备管理和能耗控制等方面的应用。同时,结合实际案例分析了这些优化算法如何提高冶金生产的智能化水平,实现安全、经济、环保的生产目标。
【关键词】冶金自动化;优化算法;生产调度;设备管理;能耗控制
引言
冶金工业作为国家经济和基础设施建设的关键支柱,其生产过程中涉及多个复杂的环节,从原料的采购、熔炼、成型到最终的检验和交付,各个环节都对生产效率、产品质量和安全管理提出了较高的要求[1]。随着科技的进步,冶金自动化系统日益成为提高生产效率和保障质量的重要途径。因此,如何通过智能化的手段优化冶金自动化系统,确保生产过程高效、经济和安全,成为行业内亟待解决的问题。
在这一背景下,本文探讨冶金自动化系统的构成及其优化目标,重点分析优化算法在生产调度、设备管理与能耗控制等方面的应用。通过对相关技术的深入剖析,旨在揭示优化算法如何提升冶金生产的智能化水平,实现生产过程的安全、高效和环保。本文还将结合实际案例,展示优化算法在冶金企业中的成功实践及其取得的显著成效,从而为冶金行业的持续发展提供理论基础与实践指导,以推动其向更加智能和可持续的方向发展。
一、冶金自动化系统的构成
冶金自动化系统通常是一个复杂的集成系统,涵盖了多个子系统,这些子系统共同作用,确保冶金生产过程的高效、稳定和安全。主要构成包括生产监控系统、过程控制系统、数据采集系统和设备管理系统等[2]。
(一)生产监控系统
生产监控系统负责实时监测生产过程中的各种参数,如温度、压力、流量等。这一系统通常配备多个传感器,能够将实时数据传输至中央控制平台,通过可视化界面让操作人员直观了解生产状态。此外,先进的监控系统还配备了数据分析和故障预警模块,能够及时发现设备异常,提高操作人员的响应速度。
(二)过程控制系统
过程控制系统是冶金生产中关键的环节,负责对生产过程进行自动调节,以保持所需的操作条件。这一系统通常采用比例积分微分控制(Proportional-Integral-Derivative Control,PID)和模糊控制等控制策略,根据生产情况自动调整控制变量,确保产品质量和生产效率。例如,在炼钢过程中,需要精确控制炉温和冶炼时间,以获得符合标准的钢材。
(三)数据采集系统
数据采集系统通过各种传感器和监测设备,实时采集生产过程中的数据,并将其传输至中央数据库。数据的准确性和实时性对于后续的过程分析和决策具有至关重要的影响。随着物联网技术的发展,数据采集系统也在不断演变,以实现更高效的数据采集和存储。
(四)设备管理系统
设备管理系统负责对冶金设备的运行状态进行监控,包括设备的使用率、故障率和维护计划等。通过对设备状态的分析,管理人员可以及时制定维护策略,预防设备故障,并合理安排生产,避免因设备故障而导致的停产损失。
二、优化算法在冶金自动化系统中的应用
(一)冶金自动化系统的优化目标
1.提高生产效率
随着市场竞争的加剧,冶金企业面临着日益严峻的生产效率要求。合理的生产调度与控制不仅能够显著提升生产速度,还可以减少设备闲置和等待时间[3]。通过应用优化算法对生产流程进行合理规划,可以实现生产线的最优排程,涵盖了原材料的储存、加工、运输、设备运行等多个方面,从而提升整体的生产效率。
例如,在钢铁制造中,通过对炼钢和轧制过程进行优化调度,可以最大程度地减少设备之间的空闲时间,提高每台设备的利用率。采用遗传算法对不同轧制阶段进行智能调度预测,可以将冶炼炉的出钢时间与轧制线的进钢时间高度匹配,使得生产连续性得到保障,整体生产效率因此提高了15%到20%。除生产调度之外,也要关注工艺参数的优化配置。例如,合理调整炉内温度和化学成分,减小温度波动幅度,增强冶炼过程的稳定性,从而使生产流程更加顺畅,提升整体生产效率。
2.降低能耗
冶金生产通常是一个高能耗的过程,能源费用占据了生产总成本的相当一部分。因此,优化能耗成为企业的重要目标之一。通过对生产过程中的能源使用情况进行精细化管理,利用先进的算法分析历史数据、预测能耗需求,并制定合理的能耗管理策略,能够有效降低冶金生产中的能量消耗[4]。这不仅有助于企业节省成本,还有助于提升社会整体的资源利用效率,推动绿色冶金制造。
在现今光纤,嵌入式传感器等先进技术的基础上,冶金企业应建立吨钢能耗的监测体系,通过智能控制系统进行实时监测,以及定期利用能量管理系统进行数据分析,找出能耗偏高的环节,加以优化[5]。例如,在钢水输送过程中,优化泵的使用方式和调节阀的位置可以节省20%的能耗。此外,采用先进的能效优化算法,如粒子群优化(Particle Swarm Optimization,PSO)算法,从燃料配比和加热模式等方面实现能效改进,可减少能耗的同时提高产值。这不仅有助于企业节省成本,还能提高其对环境的可持续发展贡献。
3.提升产品质量
产品质量的好坏直接影响着企业的竞争力。随着消费者对产品品质要求的不断提高,冶金企业需要在产品的一致性和稳定性上下功夫[6]。优化算法能够帮助企业在关键控制点进行实时数据分析,对生产过程进行动态调整。例如,通过在线监测材料温度、成分等参数,采用反馈控制策略,确保冶炼过程稳定在最佳工艺窗口内,从而提升成品质量。
以钢铁生产为例,在炼钢过程中,使用模糊控制器对炉内的化学成分变化进行实时监测和调整。通过对材料成分的分析,可以及时修正炉料比例,控制出钢的成分,使得成分的波动控制在标准范围之内,提高成品的合格率。另外,借助机器学习和深度学习技术,结合历史生产数据和产品质量数据,对炼制和轧制过程中各个环节进行综合优化,分析影响产品质量的各个因素,减少不合格品的产生,提高整体质量管理水平[7]。
4.确保安全生产
安全问题在冶金行业尤为重要,生产过程中的各种突发事件可能导致人身伤害和设备损坏。因此,优化冶金自动化系统的安全管理也是一项重要目标。利用先进的预警系统和智能监控技术,可以有效识别和监测潜在的安全隐患。结合数据分析,管理者能够做出迅速反应,降低安全事故发生的可能性。同时,通过建立和完善事故预警机制,进一步提升企业的安全管理水平。
在安全系统设计中,通过引入基于风险评估的决策支持系统(Decision Support System,DSS),可以有效整合数据,提升安全监管的精度与效率。例如,在大规模的冶金作业中,通过传感器监测温度、压力和振动等关键指标,结合实时数据分析,建立实时安全监测系统。该系统能够及时预警和处理潜在事故风险,同时通过详细的故障分析与学习机制,逐渐优化安全管理策略[8]。此外,定期进行安全培训和应急演练也是确保安全生产的重要一环。通过将优化管理策略融入企业文化,增强员工的安全意识,从而把安全风险控制在最小,确保冶金生产的安全性和可持续性。
(二)冶金设备管理系统的优化
设备管理系统是冶金自动化系统中的重要组成部分,涉及设备的运行监控、维护计划和故障预测等。优化设备管理系统有助于减少停机时间,提高设备的可用性和生产效率[9]。
1.实时监控
通过安装智能传感器,对设备进行实时监控。传感器可以监测设备的运行状态、温度、振动及压力等关键参数,形成数据反馈。借助物联网技术,实时数据能够传输至云平台,供数据分析使用。实时监控系统能够为设备运行提供数据支撑,当异常情况发生时,则可以通过应用程序自动生成预警,减少设备损坏和生产停滞的风险。
2.故障预测
运用机器学习和大数据分析,可以对历史数据进行深入挖掘,识别故障模式并进行预测。设备发生故障往往具有一定规律,分析设备历史运行数据,可以挖掘出潜在的故障情况,实施预测性维护。这种方法不仅可以有效降低因设备故障带来的停机损失,还能降低维护成本,提高设备利用率。
3.优化维护计划
传统的设备维护多为定期维护和故障修复,并不能完全保证设备的高效稳定运行。通过引入优化算法,如多目标优化算法,可以针对设备的运行状态、生产计划和维护条款,综合考虑相关因素,制定科学合理的维护计划。这种动态维护策略可以确保设备在最佳状态下运行,降低突发故障风险。
(三)冶金生产调度的优化
生产调度是冶金生产中的关键环节,直接影响生产效率、资源利用以及交货期。采用先进的优化算法可以为生产调度提供有效的解决方案。
1.调度算法的应用
生产调度需要考虑多种因素,如设备能力、工艺流程、材料供应等。遗传算法、粒子群优化算法等都可以用于解决冶金生产调度问题。通过对任务优先级和处理时间进行建模,优化算法可以快速生成最优调度方案。例如,结合生产任务的加工时间与设备的可用性,利用遗传算法进行调度优化,可以减少设备转换时间,提升生产线的整体利用效率。
2.动态调整
在实际生产过程中,突发的设备故障、材料短缺或订单变更等情况都可能对调度带来影响。采用动态调度算法,可以实时监控生产状况,并根据实时数据进行调度方案的调整。这不仅提高了生产的灵活性,也能有效应对生产过程中出现的变化。通过在调度系统中引入机器学习模型,逐步调整和优化生产计划,可以在不增加资源投入的前提下,提高生产的响应速度和整体效率。
3.集成优化
集成优化可以将生产调度与其他环节(如质量控制、能耗优化等)结合在一起,形成一个全面的优化体系。通过系统工程的视角,创建整体模型,综合考虑多个目标和约束条件,使得生产调度的优化不仅局限于单一目标,还可扩展至多个领域的动态协调。这样的集成优化能够从系统层面实现生产能力的全方位提升。
4.生产调度与库存管理的协同
在冶金行业中,库存管理是影响生产效率和成本的重要因素。通过实现生产调度与库存管理的协同优化,可以确保原材料和半成品的及时供应,减少库存积压和浪费。利用先进的信息技术,如射频识别和物联网技术,实现库存的实时监控和追踪,结合生产调度系统,进行动态库存管理,提高库存周转率和资金利用率。通过预测分析,提前制定采购计划和生产计划,避免生产中断和供应链风险,进一步提升企业的竞争力。
结语
综上所述,冶金自动化系统的优化是实现高效、安全、环保生产的关键。通过引入先进的优化算法,能够有效提升生产效率、降低能耗、保障产品质量并强化安全管理。本文分析了冶金自动化系统的主要构成和优化目标,探讨了优化算法在生产调度、设备管理和能耗控制等方面的应用,显示出其在提升智能化水平方面的重要性。随着行业竞争的加剧和市场需求的变化,冶金企业必须不断创新,借助智能化手段提升生产能力,以维持其市场优势。未来的研究应更加聚焦于优化算法的深度融合,结合大数据分析与人工智能技术,实现冶金自动化系统的全面优化,以适应快速变化的生产环境。冶金自动化系统的优化算法不仅为企业带来了显著的经济效益,还推动了整个行业向智能化、绿色化方向发展。持续的技术革新和系统优化将是提升冶金行业核心竞争力的关键。
参考文献:
[1] 刘然,高子扬,李宏扬,等.高炉智能优化系统综述与展望[J].中国冶金,2024,34(03):13-24.
[2] 万春秋,李擎,崔家瑞,等.基于粒子群算法的精轧AGC系统智能参数优化及实验设计[J].实验技术与管理,2023,40(05):31-37.
[3] 李松涛,李维刚,甘平,等.基于Sinkhorn距离特征缩放的多约束非负矩阵分解算法[J].电子与信息学报,2022,44(12):11.
[4] 姚政,吴怀宇,陈洋.基于两阶段优化的并发流任务计算卸载策略[J].计算机工程,2022,48(12):62-71.
[5] 周晓敏,李雄,李丽琦,等.基于自适应矩估计算法的冷连轧机板形反馈优化控制策略[J].冶金自动化,2022,46(06):102-110.
[6] 金立,顾兴华,谢晟.基于人工智能模型剪枝技术在钢铁园区的车辆管理研究[J].冶金自动化,2022(S1):200-203.
[7] 陈洋,钟树成,陈志环.具有最小信息延迟的多无人机路径规划方法[J].中国惯性技术学报,2024,32(05):521-530.
[8] 夏建超,王志远,黄成永,等.考虑时空约束的炼钢区域多行车协同调度优化研究与应用[J].冶金自动化,2022(02):80-89.
[9] 刘淑杰,张磊.大型薄壁件多点位自动化柔性支撑系统的位置优化研究[J].机床与液压, 2024,52(01):115-120.
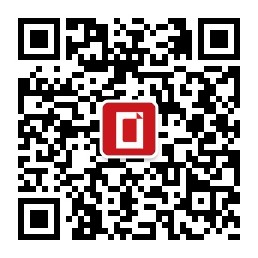