化工电气设备的检修与运维探究
- 来源:消费电子 smarty:if $article.tag?>
- 关键字:化工电气设备,检修与运维,无停机检修技术 smarty:/if?>
- 发布时间:2025-04-17 21:57
王爱青 王刚 许聪聪
【摘 要】化工电气设备的高效运维是保障化工生产安全与提升生产效率的关键。针对化工电气设备运维中故障预测困难及风险管控不足的问题,文章探讨了智能化技术在设备检修中的应用。通过分析设备故障的主要原因及运维面临的挑战,提出了智能监控与预测性维护系统的优化策略,旨在通过实时监测与数据驱动的故障诊断提升设备运行稳定性。该系统通过大数据分析和人工智能算法,能提前识别潜在故障并实施精准维修,有效延长设备使用寿命、降低维护成本,同时显著降低安全风险,为化工行业提供理论依据与实践指导。
【关键词】化工电气设备;检修与运维;无停机检修技术
引言
化工电气设备在现代化工生产中起着核心作用,其稳定性和安全性直接关系到生产效率与环境保护。近年来,随着国家对安全生产的监管要求不断强化,如《危险化学品安全管理条例》及《电力监管条例》等政策文件的出台,化工电气设备的检修与运维面临更加严格的安全与技术要求。化工电气设备的高风险特点使得其运维管理亟须创新技术手段,以实现高效、精准的故障预测与风险管控。文章将探讨现代智能化技术在化工电气设备运维中的应用,分析其在提升设备可靠性、降低安全风险方面的潜力。
一、化工电气设备的特点
化工电气设备在化工生产中起着至关重要的作用,具有高度集成性和复杂性。设备通常包括电力变压器、电动机、开关设备、传感器、仪表等,广泛应用于化工厂的生产过程中。化工电气设备的特点之一是工作环境复杂,受温度、湿度、腐蚀性气体等因素的影响较大,导致设备的使用寿命和稳定性受到较大挑战[1]。此外,化工电气设备常与其他高风险设备共同工作,如压力容器、加热炉等,存在较高的故障传播风险。其设计和运行要求具有较强的安全性和可靠性,设备必须满足防爆、防火、防腐蚀等严格要求,以应对化学品泄漏和环境恶劣等突发情况。
二、化工电气设备检修和运维工作中存在的安全风险
(一)电气触电风险
在化工电气设备的检修与运维过程中,电气触电是最常见且最危险的安全风险之一。化工厂内的电气设备通常运行在高电压和高电流下,电气系统若发生故障或操作不当,触电事故的发生概率大大增加。尤其是在设备长期运转后,电气部件老化、接线松动或绝缘损坏,都会为触电提供可乘之机。此外,化工厂的工作环境通常湿度较高,存在腐蚀性气体和粉尘等,进一步加剧了电气设备的漏电风险。
一方面,触电事故的发生通常是由于操作人员未能按照正确的操作规程进行检修或运维工作。尤其是在停电措施没有彻底落实时,设备仍然带电进行检查,或在设备外部存在电气元件裸露、接触不良等情况下,触电的风险极高。电气设备和电缆线路的老化、磨损、绝缘层破损,都会导致电流外泄,一旦工作人员接触到带电部件,就有可能发生触电。
另一方面,化工电气设备多设置在空间狭小、环境恶劣的地方,设备周围的潮湿气候、腐蚀性物质和杂乱的电线也给维修人员带来了更多隐患。在复杂环境下,操作人员的安全意识可能不够高,缺乏必要的防护装备,如绝缘手套、绝缘鞋等,加剧了触电事故的发生风险。
触电不仅会对操作人员的生命安全构成严重威胁,还可能导致设备进一步损坏、生产中断,甚至引发更为严重的连锁反应。
(二)设备起火或爆炸风险
化工电气设备在检修和运维过程中,起火或爆炸的风险是极为严重的安全隐患,尤其是在化工厂这类具有高度危险性的环境中。化工厂内,电气设备通常与易燃、易爆的气体、液体或化学品接触,若发生电气故障,极容易引发火灾或爆炸事故[2]。
第一,电气设备的过载、短路和电气部件老化是引发火灾和爆炸的常见原因。电气设备在长时间使用过程中,电力负荷可能超出设计值,导致设备过热。设备外部温度过高时,会使周围易燃物质着火。此外,电气设备中的电弧和火花也可能成为引发爆炸的源头,特别是当设备运行在有易爆气体、蒸汽或粉尘的环境中时。电气设备一旦出现故障,电弧或火花会直接与易燃、易爆气体发生反应,引发火灾或爆炸。
第二,化工电气设备通常需要在极端环境下运行,包括高温、高湿、腐蚀性气体等环境。恶劣条件容易加剧电气设备的老化,导致电气绝缘层破损、接线松动等问题,从而增加电气故障的概率。当设备老化严重,电气部件失效时,更容易引发火灾,特别是在设备操作不当或意外碰撞的情况下。更为危险的是,在密闭的环境中,爆炸性的气体可能被电气设备的故障引燃,造成更为剧烈的事故。
第三,化工电气设备的复杂性和多样性增加了火灾和爆炸发生的复杂性。设备的不同部分可能在不同的工作阶段和环境中相互作用,增加了故障传播的可能性。例如,当电气设备发生故障时,未及时断电可能导致故障扩散,迅速引发火灾或爆炸,尤其是在高压或高负荷的情况下,爆炸后果更为严重。
(三)化学品泄漏风险
化学品泄漏是化工电气设备检修与运维过程中不可忽视的安全风险,尤其是在涉及易燃、易爆、腐蚀性或有毒化学品的环境中。化工厂的电气设备通常与各种化学品密切相关,如液体化学品、气体及其他危险物质。化学品的泄漏不仅可能对设备本身造成损害,还会对员工健康、安全以及周围环境造成极大的威胁。
首先,化学品泄漏通常与电气设备故障或操作不当密切相关。例如,在电气设备检修过程中,若操作不慎触碰到连接化学管道的电气部件,可能会导致管道破裂或连接松动,从而引发化学品泄漏。此外,设备长时间未进行检查与保养,可能导致老化的电缆、开关或接头漏电,电气火花或高温可能引发化学品容器的破裂或泄漏,造成严重的安全事故。特别是在电气系统未进行充分隔离和防护时,设备故障不仅可能触发火灾或爆炸,还可能导致有毒气体泄漏,进一步加剧事故的危害。
其次,化工电气设备多设置在高危区域,尤其是含有易燃、易爆气体或液体的区域。电气设备的检修过程中,一旦处理不当,可能导致危险化学品泄漏并与电火花、电弧等产生反应,引发火灾或爆炸。在这些区域内,电气设备本身的泄漏、损坏或故障不仅是直接的设备隐患,更是间接导致化学品泄漏的重要因素。
最后,化学品泄漏还可能受到环境条件的影响。例如,化工厂的潮湿、高温或腐蚀性气体环境,使得电气设备的绝缘性能和密封性下降,增加了电气设备故障导致化学品泄漏的可能性。同时,环境中存在的粉尘或化学残留物,也可能与电气设备产生的电火花或高温反应,导致更加复杂的化学反应和泄漏风险。
三、化工电气设备运维与检修工作的优化及创新
(一)应用智能化诊断技术,预测性维护创新
在化工电气设备的运维与检修工作中,智能化诊断技术与预测性维护的创新应用正逐步成为提高设备可靠性、延长使用寿命、降低维修成本的重要手段。某化工企业于2021 年引入了基于智能化诊断技术的预测性维护系统,有效改善了设备管理模式。引入前,该企业的传统维护方式依赖于定期巡检和设备故障后的反应性修复,导致设备故障率较高且维修成本较大。每当设备发生故障,生产线停机时间平均为2 天,且每年因设备故障造成的停机损失高达50 万元。
引入智能化诊断技术后,企业在关键设备(如变压器、电动机和泵)上安装了传感器,实时监测电流、电压、温度、振动、噪声等运行数据。数据通过工业物联网(Internetof Things,IoT)传输至中央数据平台进行处理,平台基于人工智能(Artificial Intelligence,AI) 和机器学习(MachineLearning,ML)算法进行分析,形成设备的健康报告,并能够识别设备的工作异常,提前发出故障预警。以电动机为例,当温度超过设定阈值或振动幅度异常时,系统会通过预警通知运维人员检查设备。此时,维护人员可及时调整电动机的负载或进行必要的冷却措施,从而避免了设备因过热或振动引发的故障。
在传统维护模式下,设备故障通常在出现明显问题后才会修复,导致设备停机频繁,且修复时间长。与之相比,智能化诊断技术能实现实时监控,通过提前识别潜在故障隐患,避免了突发故障的发生。比如,变压器的油温、负荷和电压等关键参数被实时监测。传感器在油温升高或电压波动时发出预警,系统结合历史数据和环境因素,基于数据驱动算法预测设备可能的故障,并提前通知运维人员进行维修或更换。与传统的定期维护模式相比,预测性维护技术减少了过度维护和无效停机。
根据实施后的数据,智能化诊断技术和预测性维护系统有效减少了设备停机时间。过去,每年设备故障导致的停机时间为24 小时,采用智能化诊断技术后,停机时间减少至8小时,故障率下降了35%。同时,维修成本也降低了20%,尤其是在电动机和变压器等高价值设备的运维中,系统有效地避免了不必要的维修,延长了设备的使用寿命。通过智能化诊断技术与预测性维护,企业不仅提高了设备的运行效率,也提升了运维的精细化和智能化水平。与传统的维护模式相比,该技术展现了极大的优势,减少了突发故障和停机时间,优化了设备管理和资源配置,提升了企业的生产效益。
(二)应用电气安全监测系统,实时风险预警机制
在化工电气设备运维中,电气安全监测系统(ElectricalSafety Monitoring System,ESMS)已成为确保设备稳定运行和人员安全的关键技术。以某大型化工企业为例,该企业在未采用电气安全监测系统之前,设备的故障检测依赖于人工定期检查和传统的事故后修复方法。然而,此种传统方法存在诸多局限性,故障隐患通常在设备出现严重问题之前未被发现,导致频繁的设备停机和高额的维修费用[3]。
为提高设备的可靠性和安全性,该企业于2022 年引入了基于传感器集成的电气安全监测系统。该系统采用了电压、电流、温度、振动、绝缘电阻和气体泄漏等多种传感器,能够实时监测关键电气设备的工作状态。例如,在某变压器中,系统通过电压和电流传感器实时监控设备的负载情况,确保其运行在安全参数范围内。温度传感器监控变压器内部温度,并通过内置算法实时计算温升趋势,提前发现过热迹象,防止因温度过高而导致的设备损坏或火灾。技术实施过程中,企业在变压器、电动机和压缩机等关键设备上安装了高精度传感器,并将采集的数据通过工业IoT 平台传输到中央监控系统。系统通过先进的AI 算法分析实时数据,结合历史运行记录,计算设备的健康指数,形成完整的设备状态报告。一旦设备运行参数接近预设的安全阈值,系统便会发出预警信号,提示运维人员采取相应的预防措施。
与传统的定期检查和故障后维修相比,电气安全监测系统提供了一个实时的、全面的监控解决方案。以某电动机为例,采用该系统后,在过去的12 个月内,该电动机因故障停机的时间从以前的每月2 次减少到零,并且维修成本减少了35%。
此外,振动监测技术在电动机和压缩机的运维中也发挥了关键作用。传统方法通常依赖人工巡检来发现设备的振动异常,然而,此方法通常难以实时发现问题。采用振动传感器后,系统可通过频率分析和振幅变化及时发现设备的不平衡、松动或老化等问题,提前采取维修措施,减少了设备突发故障的发生。数据显示,在引入振动监测后,该企业的设备故障率减少了28%,设备停机时间缩短了20%。
(三)应用无停机检修技术,提高设备运维效率
无停机检修技术在化工电气设备运维中的应用,已经成为提高设备运行效率、降低停机损失的关键技术手段。该技术结合了在线监测、带电作业和局部修复等手段,通过精确监控设备的运行状态,确保设备在不完全停机或局部停机的情况下完成检修,从而减少了生产中断时间,保证了生产的连续性和稳定性。
在线监测技术是无停机检修的核心组成部分。通过对电气设备的电流、电压、温度、振动等关键参数进行实时采集,并结合故障诊断模型,如基于支持向量机(Support VectorMachine,SVM)和神经网络(Artificial Neural Network,ANN)的预测算法,能实时检测设备潜在的故障风险。设备健康评估函数能根据采集到的数据分析设备的健康状态,并提前发出故障预警,指导运维人员及时采取维护措施,避免设备故障导致的停机。
带电作业技术则在高压电气设备的运维中得到了广泛应用。通过电气安全分析模型,确定设备检修过程中的安全电流和电压范围,保证维修人员的操作安全。带电作业使设备在不切断电源的情况下进行检修,尤其适用于配电变压器、电缆连接和开关柜等电气设备的日常维护,避免了传统检修方式中的停机损失。
结合以上先进技术,运维人员可在设备未完全停机的情况下进行实时监控和精准修复,从而显著提高了设备运维效率。实验数据显示,引入无停机检修技术后,设备的停机时间减少了约25%,而运维效率提升了30%。通过精确的健康评估与实时数据分析,该技术有效提高了设备运维的精细化和智能化水平,体现了其在化工电气设备管理中的巨大应用价值。
结语
化工电气设备的检修与运维工作是保障生产安全和设备可靠性的核心环节。随着智能化技术的深度融合,基于物联网的实时监测、人工智能驱动的故障预测以及自适应维护策略的应用,正推动行业从被动响应向主动防控转型。通过多维度数据融合与智能分析,系统可精准捕捉设备劣化趋势,实现隐患的早期干预,显著提升运维效率与安全性。未来,随着数字孪生、边缘计算等技术的进一步发展,化工电气设备管理将迈向更高效的智能化协同模式,形成全生命周期闭环管控体系。这不仅能够最大限度降低非计划停机风险,还将为化工生产的集约化、绿色化发展奠定技术基础,实现安全性与经济性的动态平衡。
参考文献:
[1] 田元贵.化工企业防爆电气设备选型及常见使用隐患[J].中国安全生产,2024,19(09):62-63.
[2] 崔琦.电力电气设备的维护检修技术探讨[J].中国设备工程,2024(17):170-172.
[3] 康勃.化工电气设备检修及运行维护要点分析与研究[J].全面腐蚀控制,2024,38(07):47-49.
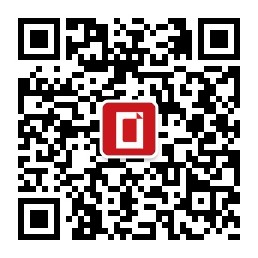